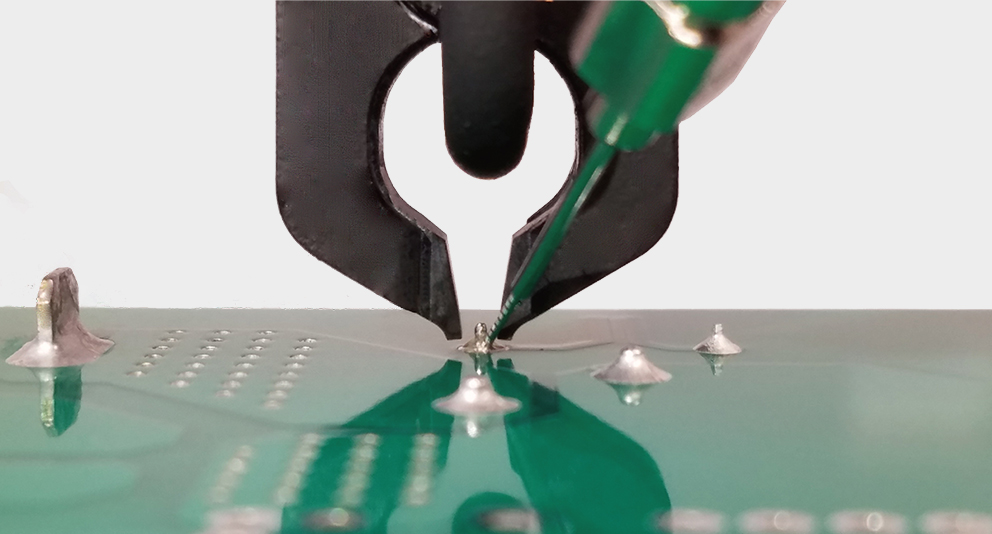
1. "Non-contact" and "various" soldering allows for a wide variety of soldering.
2. Design and commercialization of automatic soldering equipment incorporating IH (electromagnetic induction heating) technology
3. Greatly reduces CO₂ emissions and contributes to carbon neutrality
What is IH (Induction Heating) method soldering?
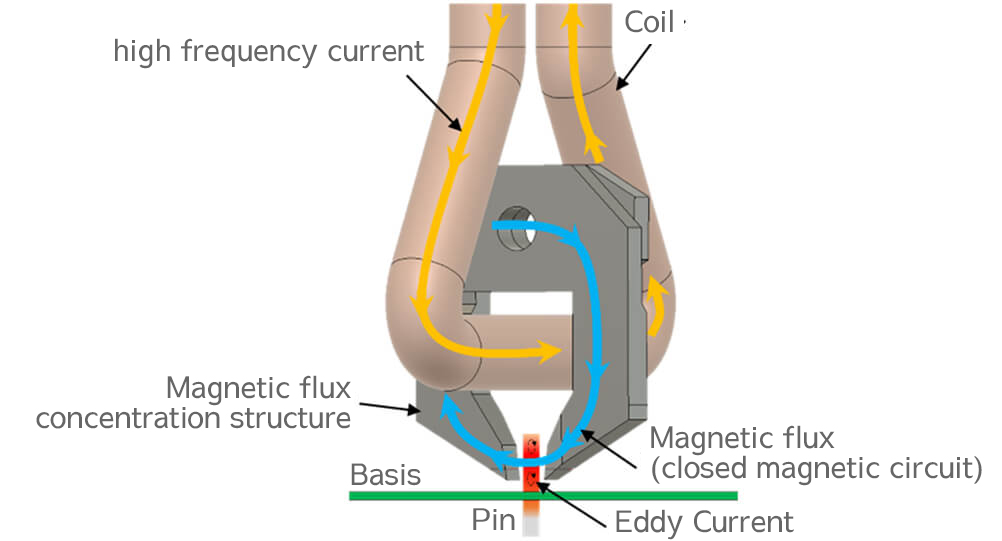
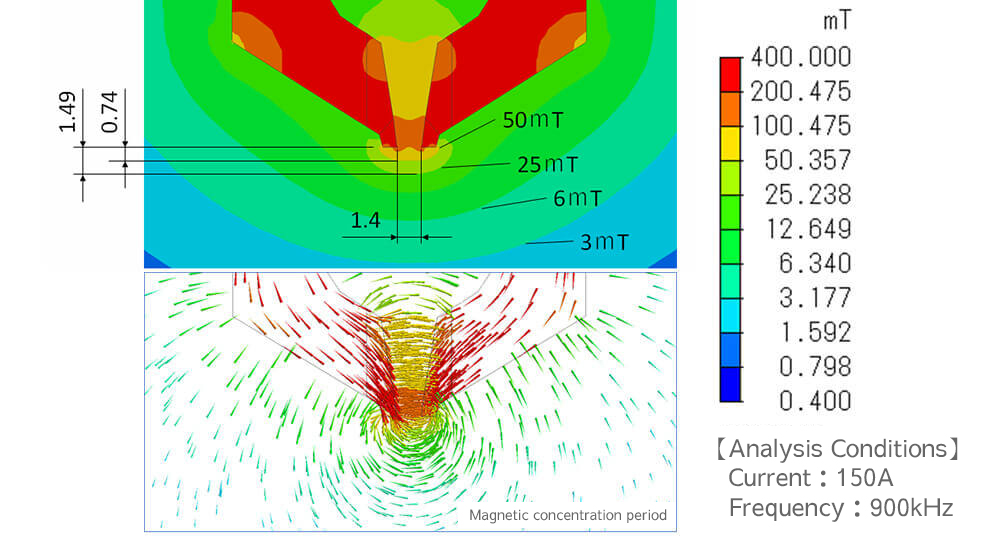
In electromagnetic induction heating, the magnetic flux density is increased in the ferrite core (magnetically concentrated structure) placed around the coil with a high-frequency current, and by placing a magnetic terminal (the pin in the above image) in a partially cut-out gap of the core, a spiral induction current is generated in the pin that flows in a direction that cancels the magnetic flux.
The current goes through the resistance of the pin’s material, and generates Joule heat on the surface.
As a result, the terminal is heated to the temperature at which solder melts, thus enables soldering.
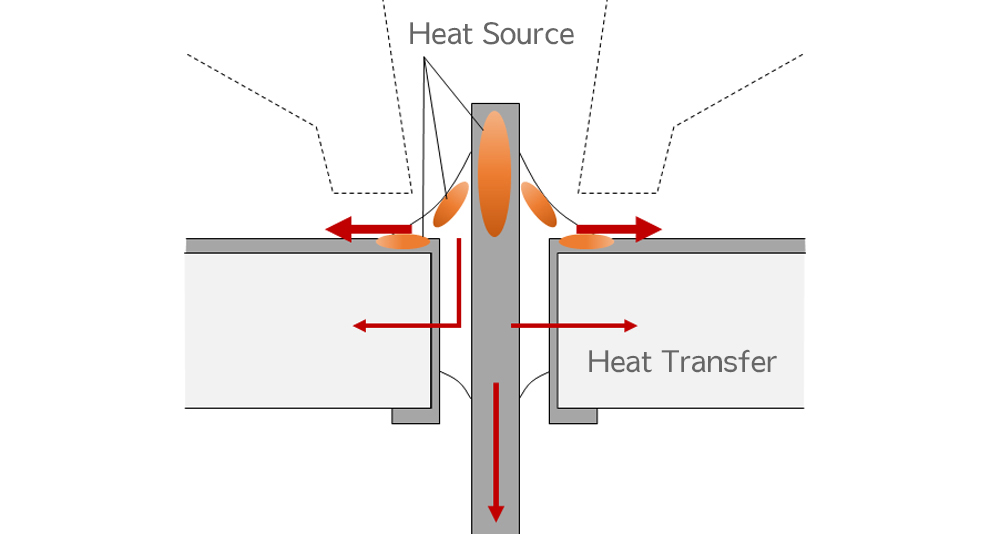
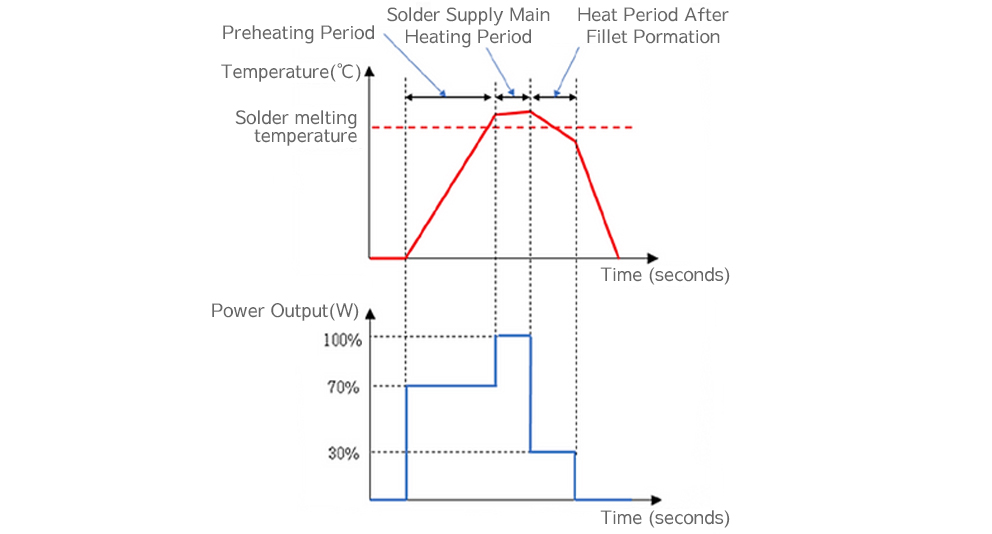
Current control enables fast control of heating intensity and allows detailed setting of pre/main/post-heating durations and temperatures.
The non-contact soldering method using IH can solder parts with large thermal capacities and low heat resistance, while contributing to carbon neutrality because it has lower power consumption compared to other methods. In addition, the ferrite core temperature at the heating tool tip is as low as 100°C or less, and the ambient magnetic field level is also kept low, ensuring safe use.
Advantages of non-contact soldering
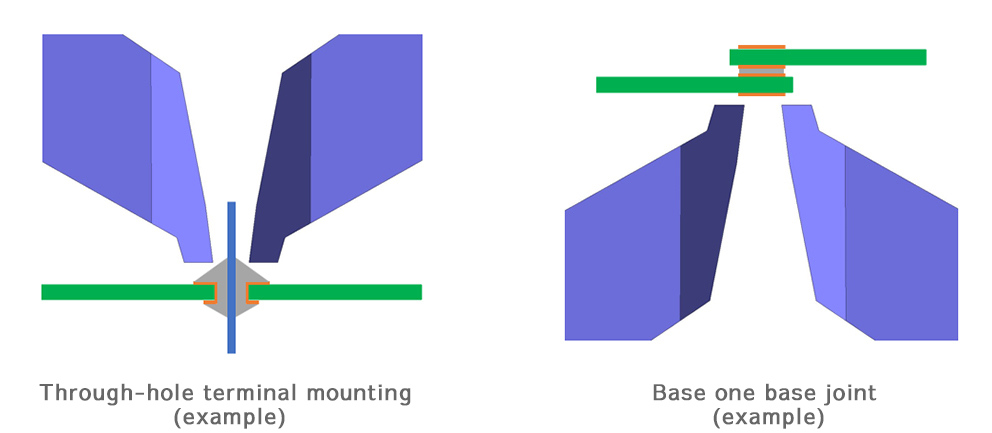
- Local heating of only the target metal part minimizes the effect on the surrounding area and the damage to the resin material.
- Detailed heating profiles can be set by current control to match the thermal capacities of different components and board pattern arrangements.
- A single tool can be used for boards containing bridge diodes, IGBTs, current sensors, and heat-sensitive nylon connectors, all of which are difficult to heat.
- Local soldering can be performed afterwards using cream solder.
- Soldering from the back side is possible with IH heating even in narrow spaces or surface joints where soldering from the component mounting side is difficult.
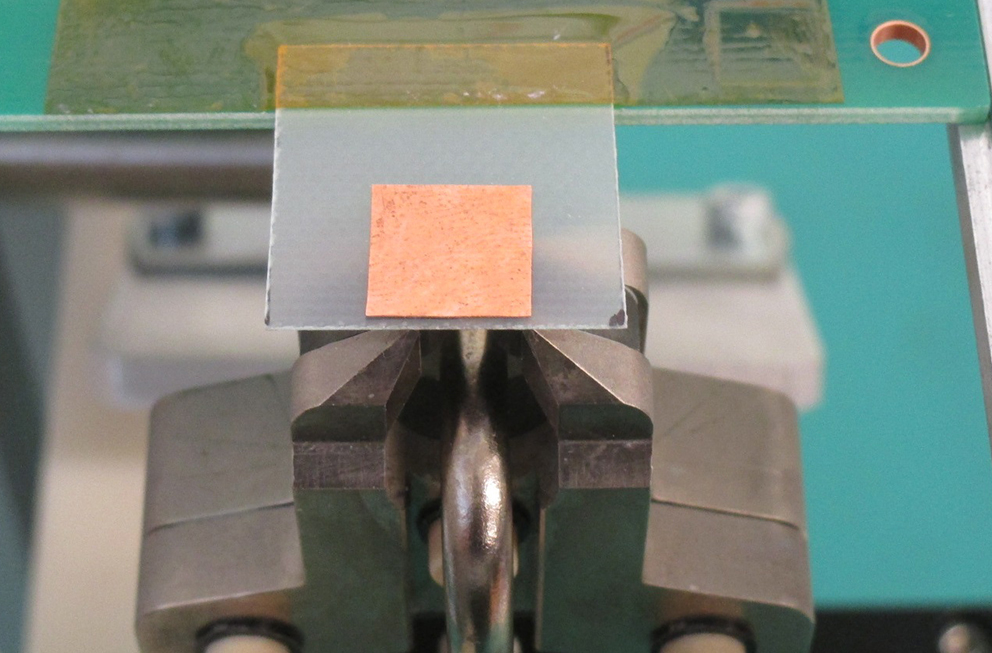
1.Heat a copper pattern of □10 x 0.1 mm with a clearance of 0.5 mm from the bottom of the base material
2.Substrate thickness: 0.3mm
3.Clearance between head and substrate: 0.2mm
→ At IH=90%, reaches 250°C in 2.8 seconds
Safe, high quality, easy maintenance
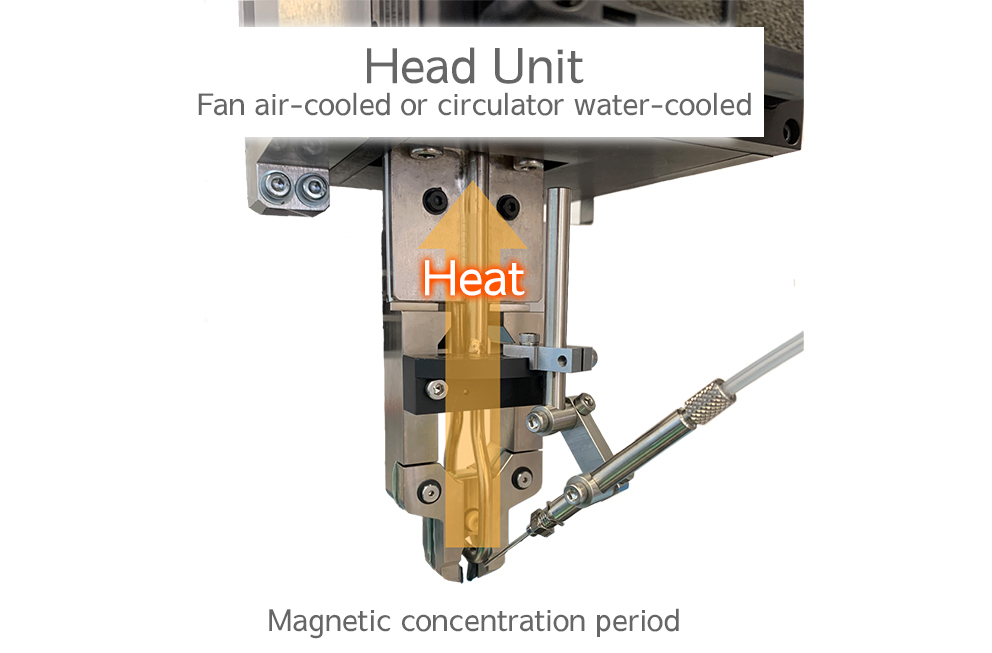
- Reduced solder ball generation and beautiful finish with fixed quantity solder.
- No wear parts, greatly reducing maintenance man-hours and automating the soldering process.
- Safe soldering environment due to suppression of electromagnetic radiation in accordance with International Commission on Non-Ionizing Radiation Protection (ICNIRP) guidelines.
- Unlike flow and reflow soldering, the workpiece cooling process, which was previously required, is no longer necessary, leading to shorter cycle time.
- Not only water cooling with a chiller, which is suitable for mass production, but also air cooling is available as an option for experimental environments. (*1 / *2)
*1 Conventional industrial IH requires several KW of power, and water cooling has been recommended for cooling the heat generated by the large current flowing through the IH coil. Since chillers with temperature control functions and water circulators are required, the equipment
tends to be large, and there is also the problem of
noise, and in some cases, the testing and introduction of IH has been postponed due to management and operation concerns. However, the IH soldering equipment we use has a maximum current of 150A, so air-cooling systems can also be selected, allowing us to offer proposals that better meet customer needs.
*2 Compared to water-cooling, air-cooling requires longer cooling time for the tools, so the number of tools per unit time (number of production) will be reduced.
Contribute to carbon neutrality
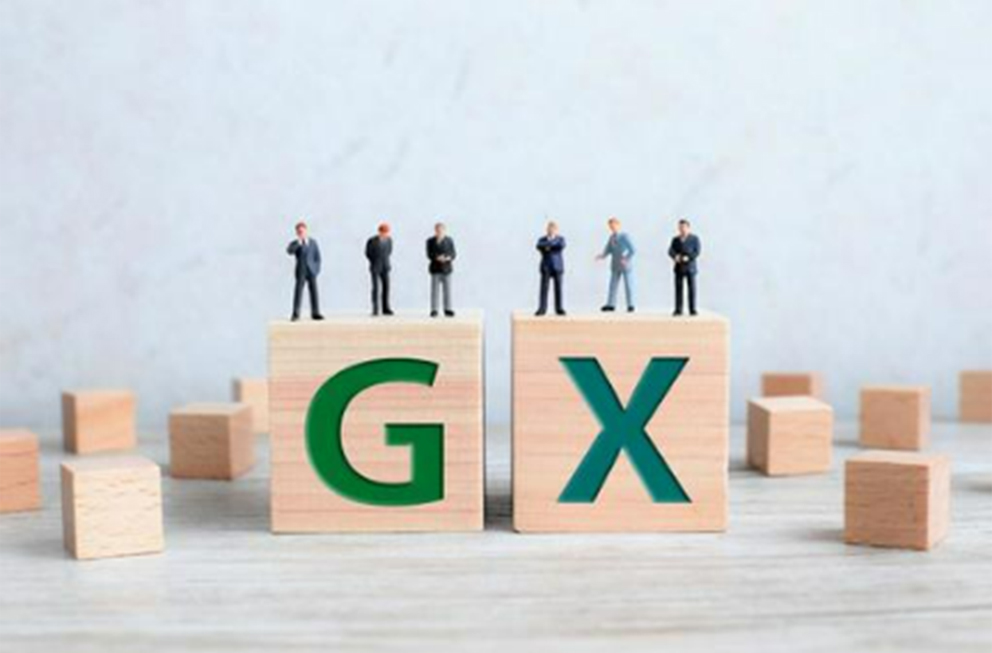
- Contributes to reduction of disposal costs by improving yield rate.
- No need for frequent replacement or adjustment of consumable parts.
- Low power consumption due to unique heating method and high-efficiency inverter control.
- Reduces CO₂ emissions and helps achieve the global goal of a sustainable development and production environment.
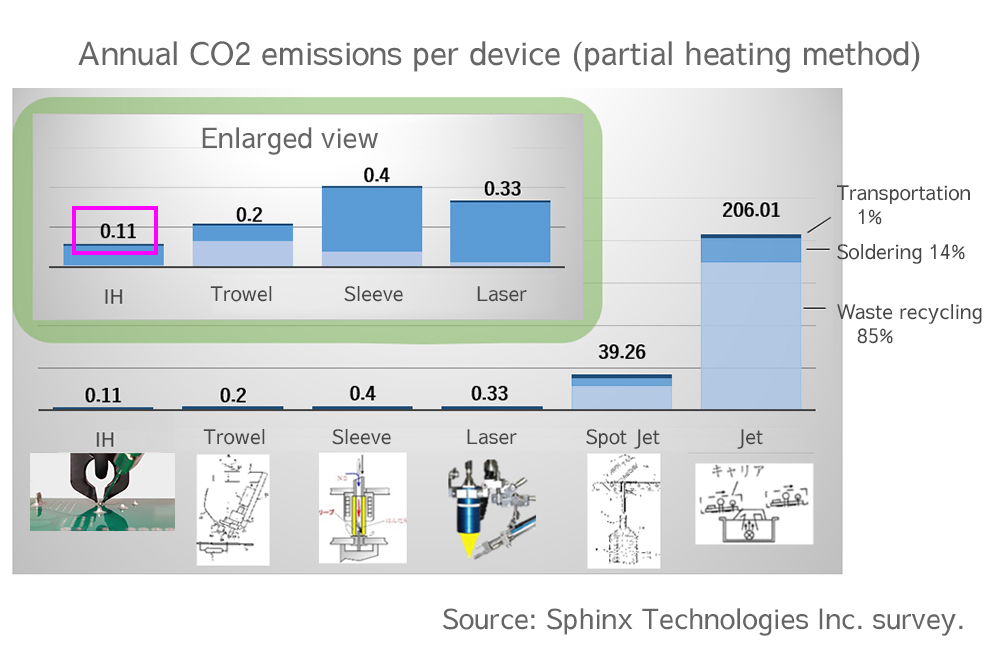
Examples of Expected Application Fields
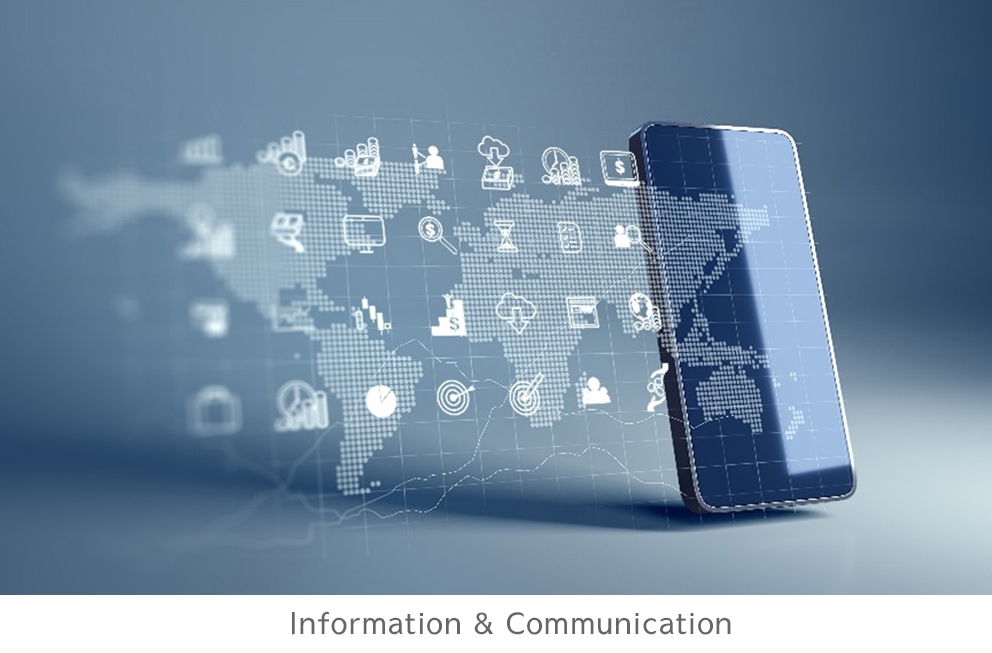
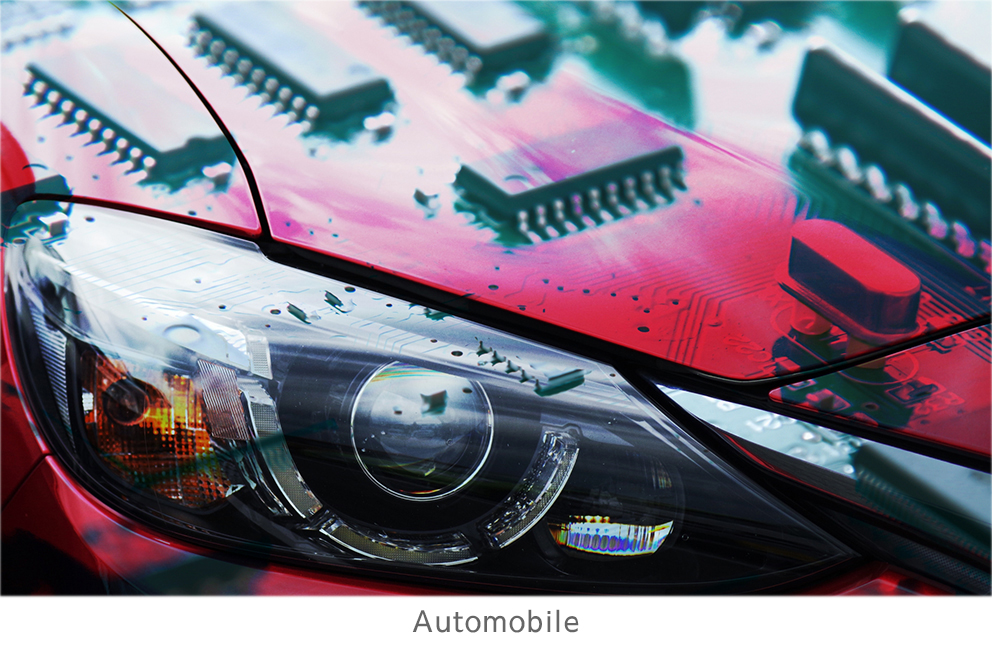
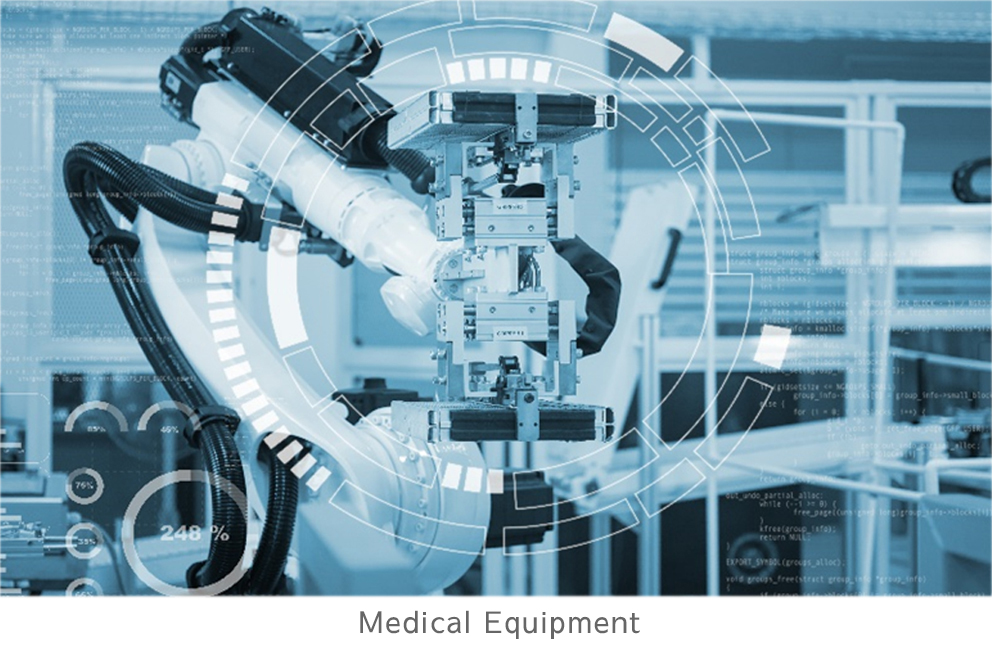
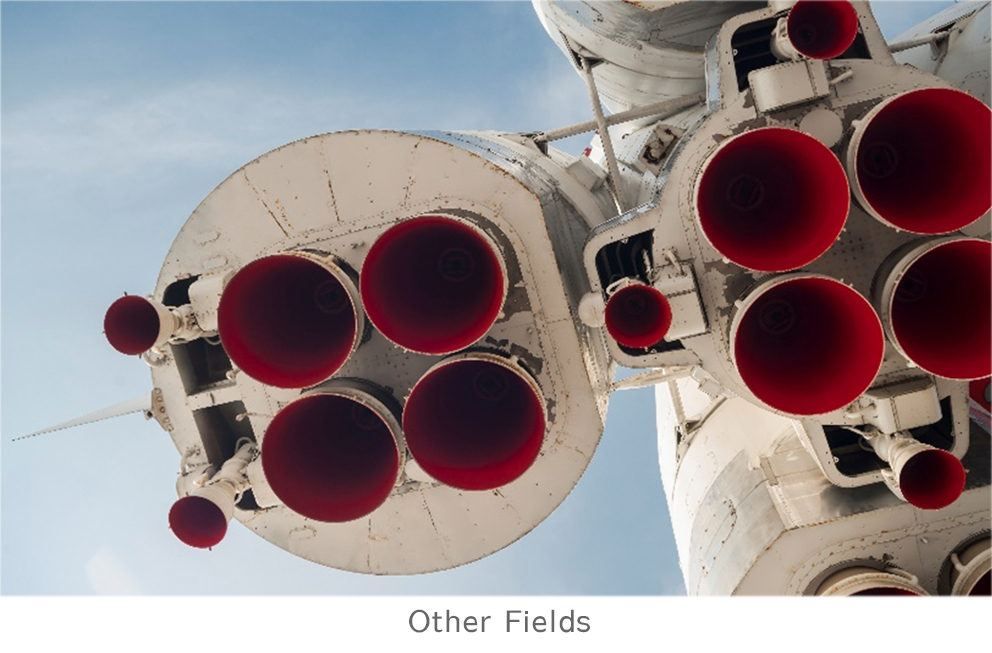
Examples of Inquiries
- Looking for a soldering method that has less impact on the workpiece and mounted parts, instead of laser or reflow soldering.
- You are considering adopting a new technology to introduce to your customers.
- We are looking for an energy-saving method for in-house processes in compliance with environmental laws and regulations.
- You want to conduct a verification test to see if the IH heating method is applicable as a soldering method.
- You want to set up an automatic machine that is suited to your production line, rather than a general-purpose unit.
- We want to introduce an automatic machine that can be integrated into an in-line system for IH soldering … . etc.
Depending on the customer’s requirements and products, we will
propose automation equipment that can optimally utilize IH technology,
including process and material support.